

LEAP-1B engines for the Boeing 737 MAX are assembled at GE Aviation’s facilities in Lafayette, Indiana, while the LEAP-1A engines for the Airbus A320neo family are assembled at Safran’s Villaroche facility, located 50km south east of Paris. This lower weight, along with state-of-the-art blade aerodynamic design, contributes nearly half of the 15% fuel efficiency improvement the engine is providing.”Īt Safran, engine assembly takes place on two pulse lines that stretch 60m “The total fan system is virtually maintenance-free, reducing aircraft weight by 1,000lbs compared to the same size fan manufactured using all-metal materials. “Because of the wide-chord blade design, the LEAP fan has just 18 blades, half the number on the CFM56-5B, 25% fewer than the CFM56-7B, and 10% fewer than its competitor,” Bastin adds. This technology results in fan blades that are not only lightweight but so durable that each individual blade is strong enough to support the weight of a wide-body airplane like the Airbus A350 or Boeing 787. The final step is adding a titanium leading edge for increased durability. These preforms are then injected with resin and baked in an autoclave. The blades and case are manufactured using a proprietary process that weaves the parts in three dimensions on a loom into their final shape. Building the fan required development of new resin transfer moulding production processes, a development that has been underway at CFM parent company Safran Aircraft Engines for more than 30 years.” “This design provides a three-dimensional aerodynamic fan system that helps achieve lower fuel burn in a high flow/high bypass engine that is lighter weight and has lower noise. “The engine is the only one in commercial aviation to feature one-piece woven carbon fibre composite fan blades and fan case,” François Bastin, executive vice-president, CFM International explains. The foundation of the LEAP engine is heavily rooted in fourth-generation aerodynamic design and environmental technology, but it is the advanced materials the company has introduced in this engine that is changing the way aviation looks at jet propulsion and laying a solid technology pathway for the future engine developments. The LEAP is providing operators with a 15% improvement in fuel consumption and CO 2 emissions compared to today's best CFM engine, along with dramatic reductions in engine noise and emissions.
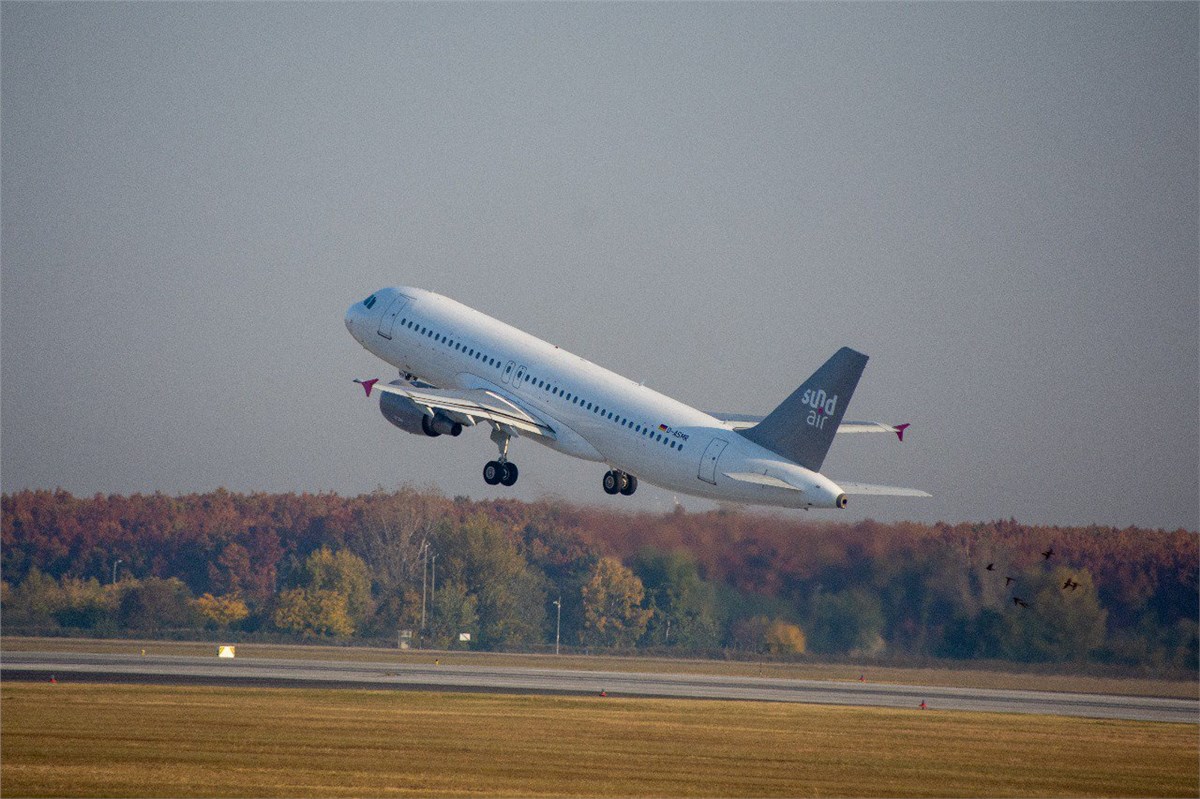
This is simply unprecedented for a new engine.” Aircraft powered by the LEAP engine are flying more than 95% of available days. “Our customers are thrilled with the fuel efficiency the engines are providing, as well as the world-class utilisation level they are achieving with this very important asset. “The LEAP engine entry into service is the most successful in our history and has been exceptional by any measure,” said Gaël Méheust, president and CEO of CFM International. Overall, this fleet has logged more than 200,000 flight hours and 100,000 flight cycles. Since then, more than 80 LEAP-powered aircraft have entered service with a total of 18 operators on four continents. The first LEAP-powered commercial flight happened on Augon a Pegasus Airlines flight from Istanbul to Antalya.
